Congrats to the Production Well-Being (PWB) Team for Earning the Q1 SelectPride Partner Award
posted on Thursday, July 25, 2019
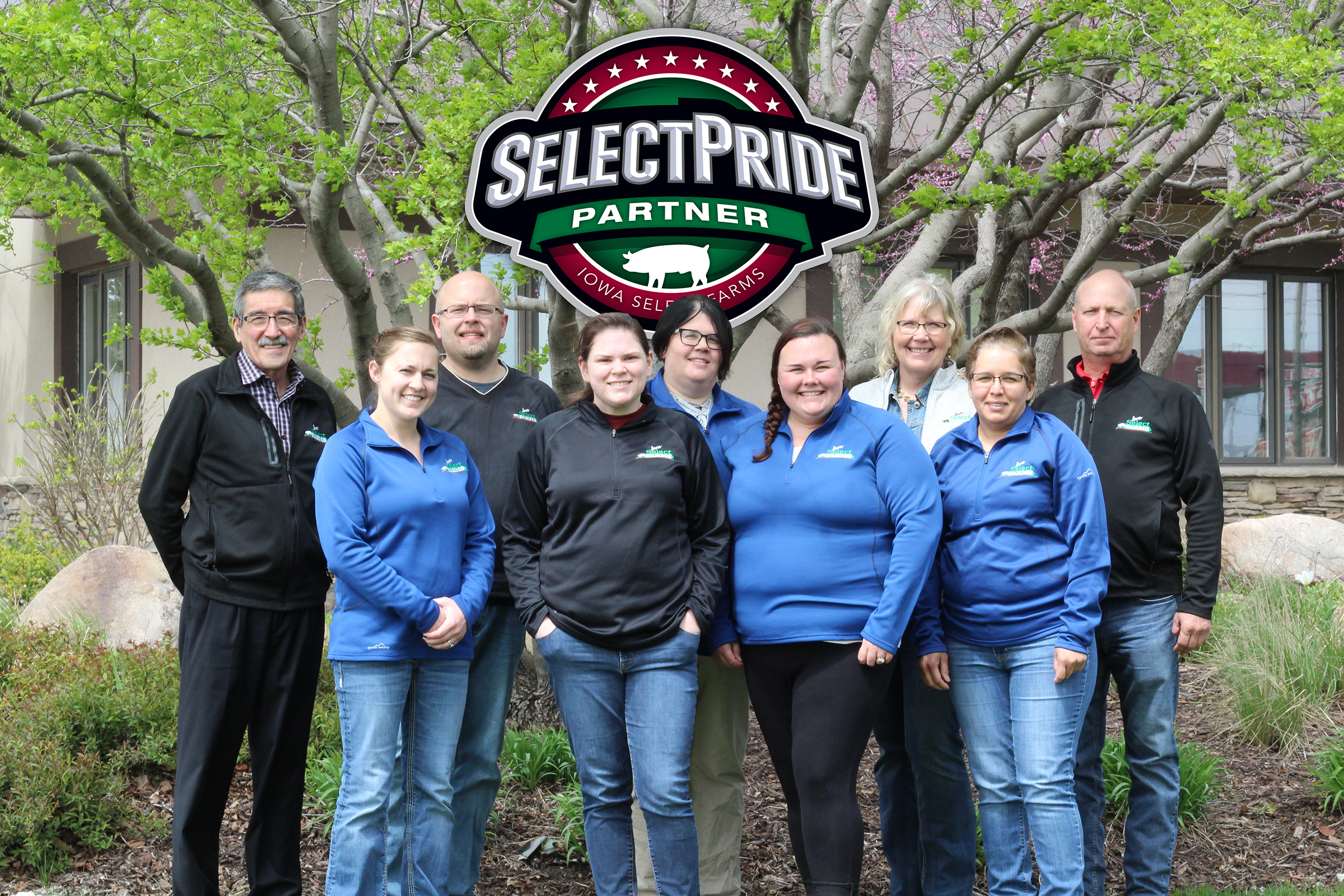
Congrats to the Production Well-Being (PWB) Team for earning the Q1 SelectPride Partner Award! Nominated by the production leadership team for their outstanding caretaker training efforts, Cassandra Jass, DVM, Director of Production Well-Being and her team of Jeff DeWeese, Craig Schrage, Tiffany Schnitker, Devin Allen, Adriana Hernandez, Pedro Garcia, Jessica Rosener and Kailey Einspahr have earned the first-ever SelectPride Partner Award.
One might assume the PWB team spends the majority of their time conducting annual and quarterly farm assessments and PQA training for all new employees, but the PWB team offers their services to provide individual and team caretaker training throughout the year. In fact, just like a request for maintenance help for a broken feed line, managers can place a ticket request for specific training on their farms.
It’s that specialized training paired with the massive, coordinated effort to organize and execute the training of 1,236 employees and hundreds of contractors across 27 different regional training sessions that earned them the winners of this inaugural award.
“You can see the thought and effort this team puts into making every interaction they have successful,” said Noel Williams, Chief Operating Officer for Iowa Select Farms. “They do a great job helping everyone find ways to get better, which improves the overall system.”
This year’s annual, company-wide training was called “Pig Problems, Every Day Decisions,” an effort designed to help caretakers make the right decisions when faced with common production scenarios where the right path forward is a little gray,” said Jass.
“You have to remember every animal is going to respond to a set of events or environmental factors differently, which is why situational education is a great approach,” said Don Hunt, sow supervisor. “The right course of action for a compromised pig may be to treat the pig, it may be to move the pig into a critical care pen, it may be a combination, or it may be to euthanize that pig right away to prevent undue pain and suffering. Throw in ten other factors the caretakers face and that’s when you can see there is no black and white procedure to follow.”
During the three-hour training, employees are split into groups and given packets of information to review with real-life scenarios that involve biosecurity, animal treatment and identification and animal handling, to name a few. Together, they offer ideas and recommendations, and collectively develop a plan and course of action.
After finalizing their plans, each group presented to the larger audience, first introducing their scenario, then shared the plan they developed. The PWB team along with the rest of the caretakers in attendance then had the opportunity to offer their expertise and validate the plans were correct, or offer a better approach. While they were presenting on their plans, members of the PWB team threw “oinks” into the group. Oinks were unforeseen obstacles or situations that were presented to the group during their presentation. These unplanned “oinks” caused them to have to react swiftly and adapt their plans.
Don says how they designed the educational sessions into smaller group sizes was really effective. “You really see a high level of engagement in the smaller groups, and everyone’s more comfortable sharing examples and contributing to the plan.”
Loni Minnick, manager at Sow 118, says she really enjoyed the training session. “I found it really interesting, and the scenarios they created were things we run into all the time.”
Tim Hermsen, senior finishing supervisor, said the training sessions for finishing managers, caretakers and contracted site managers were also well-tailored to their phase of production.
Tim says the PWB also had great decision-making insights to help caretakers determine how to prioritize their chores based on pig care. He says caretakers may encounter pigs with varying conditions while doing chores. “Each of those conditions require attention, but some more immediate than others,” says Tim. Knowing how to manage each of these conditions and the order in which to address each situation is very important.”
Tim says there are always plenty of challenges, even on a good day. “Now, add in that it’s minus ten degrees, the barn is colder than normal and the supervisor is stuck in a snowbank. You can keep throwing in as many “oinks” as you can because it will happen, and we have to be prepared and make the decisions that are the best for the pigs.”
Clint Hoversten, transportation manager, says he appreciates how the production well-being team tailored the training sessions for the truck drivers. “They’ve added sections that are specific to loading and unloading, and how to recognize and manage compromised pigs or those unfit for transport,” said Clint.
Even the employees who have been around longer appreciate the training, like Alvan Snyder, an employee of 24 years. “It’s good to keep learning things,” says Alvin. “The training team makes it fun, and because of that what they wanted us to know really sticks in our minds.”
Don says the success of the program all boils down to the people. “The PWB team brings the energy and passion to create an applicable learning experience,” he says. “They do a nice job of putting everyone at ease, and they really care about making the training experience good for everyone.”
Subscribe to our newsletter: Get fresh articles delivered straight to your inbox.
Subscribe